Inspection and detection systems continue to evolve
The need for the dairy industry to evaluate, understand these systems continues to grow.

Dairy processors are using digital reporting tools and data features to ensure food safety is not compromised. Photo courtesy of Fortress Technology
With increasing scrutiny focused on food safety, regulatory standards and to avoid food recalls, as well as wavering consumer trust in food products, dairy processors should examine their established food safety practices and systems to ensure they’re up to par.
To not only meet regulatory requirements but reassure consumers of the safety of their food and beverage products, producers must optimize their inspection and detection systems at the plant. These technologies are constantly evolving to meet the ever-changing needs of the dynamic food and beverage industries.
As the implementation date grows closer for the U.S. Food and Drug Administration’s final rule on Requirements for Additional Traceability Records for Certain Foods, there is even greater need for the dairy industry to evaluate, understand and implement high-quality inspection and detection systems as part of their robust operations.
“Stricter regulations and quality assurance standards are pushing the development of more robust inspection and detection systems that can ensure compliance,” says Mettler-Toledo Marketing Communications Manager Sarrina Crowley.
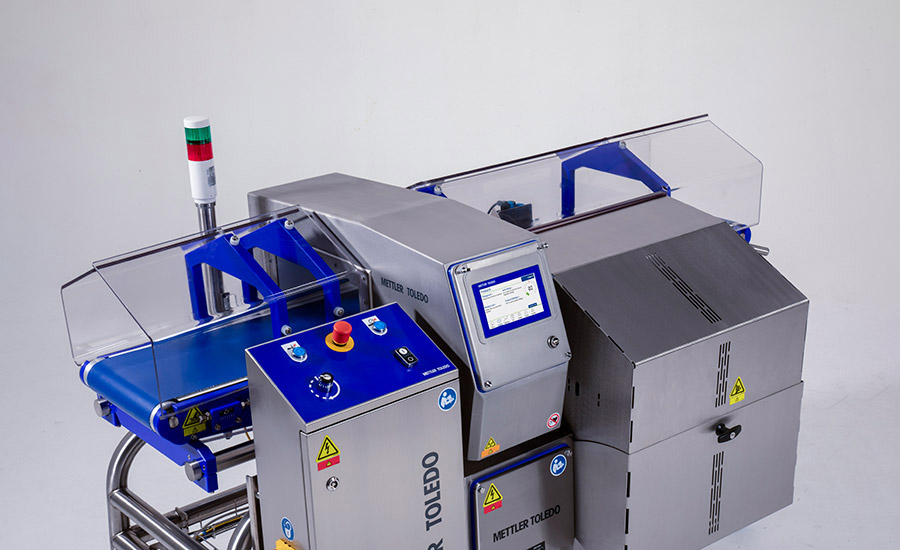
Within inspection and detection technology, artificial intelligence (AI) allows for more traceable, therefore alleged safer, food systems. As the world becomes more digitalized, AI continues to increasingly influence how the food industry operates. Now, AI can help dairy producers to meet the FDA’s Food Traceability Rule standards by increasing traceability capabilities.
Sensor technology manufacturer Baumer notes that AI capabilities present multiple benefits to consumers, such as fewer labeling errors and increased quality in consistency, as well as lowered risk for food and beverage product recalls. With weakened consumer trust in the food and beverage industry, it is essential to optimize food safety and lower risk of product recalls.
Separation technologies company Eriez sees strong potential for AI within inspection and detection equipment. Cragi Lorei, Eriez global market manager for the light industry, states, “The potential for AI-driven systems to learn from data over time offers exciting opportunities to reduce false positives and identify upstream issues in production to enhance food safety and optimize plant operations by providing actionable insights and enabling predictive maintenance.”
Multivac’s Technical Product Manager for Printing and Inspection Sinisa Dunovic notes that dairy producers are becoming increasingly interested in AI capabilities and how to best incorporate AI within their plants.
“Also important is the continued move toward increased automation in production,” Dunovic maintains. “Our customers are looking for systems that require little to no expertise and as little manual intervention as possible.”
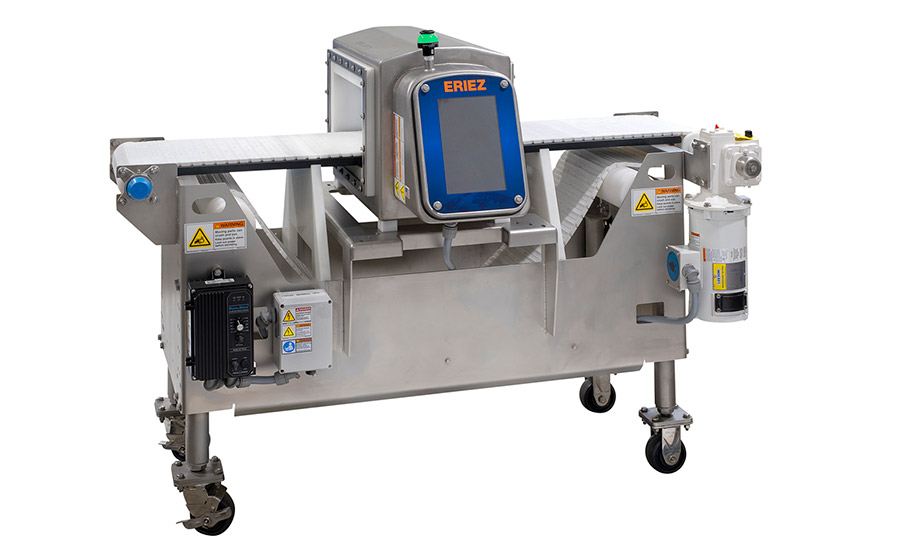
AI is — in general terms — allowing vision inspection to take over for manual inspection, which is prone to errors and worker variability, Baumer notes.
“As AI continues to evolve and the required computing power (or the cost of said power) decreases, the technology will be available to more and more processors, and fewer images may need to be trained at startup, simplifying and reducing the cost of deployment,” the company relays.
Optimizing systems at the plant
When implementing inspection and detection systems at the plant, processors should consider what they need out of their equipment. Eric Garr, regional sales manager for Fortress Technology, says that metal detectors offer high visibility and fit into multiple stages in the production process.
“They are better suited for tighter spaces, can handle higher speeds and extreme temperatures and require less maintenance compared to X-ray systems,” Garr says. “This makes metal detectors an excellent choice for both end-of-line checks and critical control points earlier in the production flow.”
Mike Palmer, senior engineer for Silgan Closures’ Equipment Division, recommends processors implement inspection and detection systems that utilize software instead of gamma rays. “By avoiding gamma technology, you can avoid the hassle of annual state fees and inspections that confirm the radiation is not leaking,” Palmer explains.
Whatever kind of equipment a processor is having installed, the equipment must be installed correctly to avoid bottlenecks or negative production impact. Robert Slauson, Advanced Detection Systems’ assistant sales manager, advises dairy processors seek startup support, as well as on-site training from their equipment manufacturer, to ensure proper installation and make sure they have informed equipment operators.
High-quality, optimized inspection and detection systems give dairy processors an all-encompassing tool to deal with problems at the plant — before they result in million dollar recalls.
“Inspection and detection systems should be a key arbiter in how successfully quality initiatives are being executed,” states Multivac’s Dunovic. “They can help you hone in on areas for improvement, such as foreign material contamination risks, without needing to be highlighted through a costly and painful recall.”
All dairy producers can contribute to a safe, secure food supply chain through process and operational optimization, Fortress Technology’s Garr affirms. One way to do this is through equipment integration: utilizing a single screen to connect all equipment.
“This setup simplifies data collection and consolidation, making changeovers faster and more efficient,” Garr notes. “By having one single interface, training and operating equipment becomes easier and safer, with cost-savings secured from faster installation, reduced training time and increased operational efficiency.”
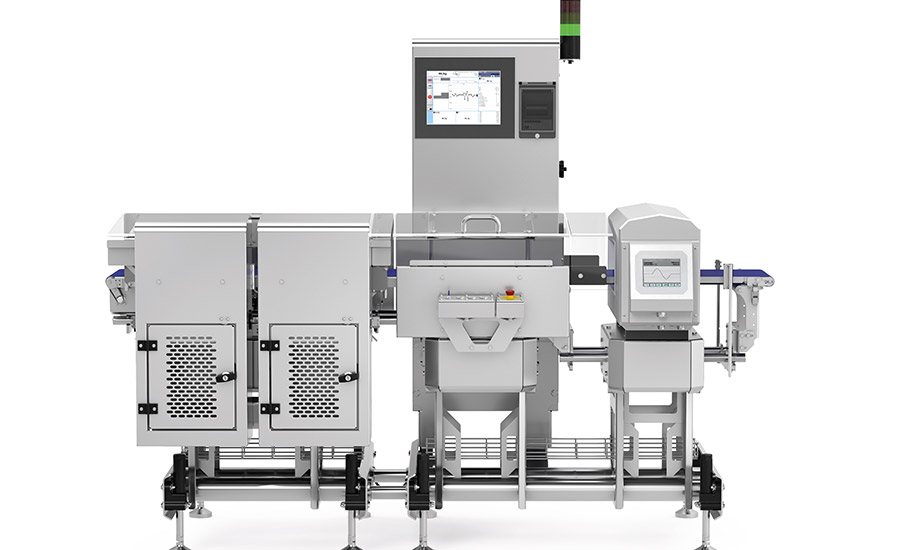
System placement is also essential for optimizing inspection and detection equipment. Eriez’s Lorei advises dairy processors strategically place metal detectors at critical stages. “This multi-stage approach detects contaminants early, protecting downstream equipment and minimizing waste,” he states.
Within system placement, processors must also consider space restraints. Crowley notes that if space is tight, processors might consider implementing combination inspection systems, which can have up to four technologies consolidated in one unit.
The future of inspection
Looking ahead, Fortress Technology forecasts stronger adoption of X-ray, vision inspection, checkweighing and metal detection in manufacturing.
“Not just as standalone systems, but with greater integration into a single integrated system,” Garr says. He adds that system integration enhances technology performance and increases production transparency, especially when considering data analytics and AI.
Increased data analytics have the potential to drive inspection and detection equipment advancements. According to Palmer, Silgan Closures is leveraging increased analytics for deeper insights and analyses of systems and the production line.
“This more accurate data will educate a dairy on improved efficiencies, reject rates, and line speeds,” Palmer says. “The system alerts will highlight hardware issues, filler issues, capper issues, system slowdowns (slower rates), and outages. The improved analytics will improve throughput.”
Garr concludes that production managers are already using data at the plant to optimize machine and human relations, utilizing data to predict rather than react during production.
Looking for a reprint of this article?
From high-res PDFs to custom plaques, order your copy today!