AI to change the future of the dairy plant
Collaborative efforts can go a long way toward meeting 2030 sustainability goals.

Photo courtesy of gorodenkoff / iStock / Getty Images Plus
Huge changes in dairy plants, which once seemed far way, are now close to coming to fruition.
Sustainability will no doubt be a big component of the plant of the future, but that is not the only thing dairy processors are envisioning. The big buzzword of artificial intelligence (AI) is sure to affect dairy plants in the future, as well as several other factors we will address throughout this story.
Several manufacturers call today’s technological changes in the dairy plant “Industry 4.0.” “Chart recorders and analog records are being replaced with digital information and offer additional protections to information,” explains Kyle Lake, product market manager at Baumer, U.S., Bristol, Conn.
The dairy industry faces an uncertain future, driven by a need to address consumer concerns, adapt to a changing workforce, and operate sustainably, Neil Smith, segment president of CPG for Schneider Electric, Rueil-Malmaison, France, adds.
“Industrial companies are increasingly turning to technologies such as software-defined automation, Internet of Things (IoT), AI, and industrial robotics to better optimize plants, empower their workforce, increase agility, and bolster innovation efforts; and the same is true for dairy processors,” Smith notes.
In fact, Smith outlines five key challenges facing the future of dairy plants and potential solutions to these issues.
- Building Trust: Consumers are increasingly demanding transparency about food safety and sourcing. With the European Union introducing the NIS2 Directive and regulations likely to tighten further, it is vital for dairy plants to implement robust cybersecurity and traceability systems, to ensure they comply and build trust with their customers. Clearly communicating ethical sourcing practices enables them to address consumer concerns proactively and demonstrate authenticity.
- Bridging the Skills Gap: Changing workforce demographics are making it increasingly challenging to attract and retain the right people. Investing in training programs and attracting younger generations to the dairy industry is key to overcoming this. This can be achieved by showcasing innovation and sustainability efforts and using advanced technologies such as AI and virtual reality (VR). The use of these technologies is key to attracting new workers as younger workers feel excitement toward using these technologies and the opportunities they present, with research showing that AI is set to create new jobs in the traditional operational technology space by reducing time spent on administrative tasks.
- Mitigating Climate Change’s Impact: The dairy industry is under pressure to reduce its environmental footprint by lowering water and energy usage. It needs to prepare for potential disruptions caused by resource scarcity. Implementing sustainable practices like closed-loop water systems and renewable energy sources harnessing automation and digital solutions that monitor energy and resource consumption and provide insights into how to reduce wastage is a vital way around this, as well as exploring alternative materials where accessibility disruptions threaten to slow down production.
- Adapting to Evolving Consumer Preferences: Dairy producers need to cater to diverse needs by producing multiple products, especially in light of the surge in demand for plant-based alternatives. Producing multiple goods in the same plant is vital for achieving this, which can require building new plants quickly or designing modular and flexible production lines. Software-defined automation makes it possible to have centralized control across the entire production line and enables the plant to use robotics to make real-time adjustments on the line to improve efficiency and optimize production flow.
- Balancing Cost and Innovation: Minimizing operating costs and downtimes while optimizing inventory management and investing in facility upgrades is a further challenge to dairy plants. They can best solve this by integrating predictive maintenance systems to reduce downtime. Predictive maintenance is key to reducing operational costs (OPEX) driving cost-efficiency, as the data insights provided enable operators to minimize equipment failure and costly downtime in advance as well as prioritize investments that extend the lifespan of existing equipment.
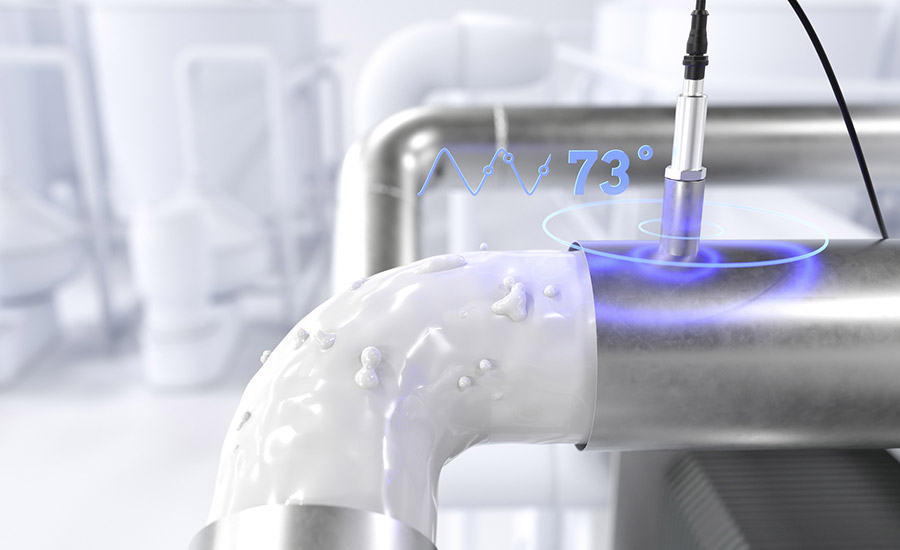
Sustainability and associated costs
Preparing for Industry 4.0 may sound great, but any new plant implementation costs money. Do sustainability upgrades need to break the bank? Lake says the answer is “no.” “With the addition of some key measuring points, [processors] can cut down on water, chemicals and monitor energy better,” he notes. “Using these devices in digital output like IO-Link allows for control as well as monitoring to look for improvements.”
According to IO-Link, it is the “first standardized IO technology worldwide for the communication with sensors and actuators. The powerful point-to-point communication is based on the long established three-wire sensor and actuator connection without additional requirements regarding the cable material.”
IO-Link could be extremely helpful in automated plants, David Medlar, vice president, valves & pumps, North America, GEA, adds. “The degree of automation in production systems in the food, dairy, pharma and beverage industries is ever on the rise. During the fast digital development toward Industry 4.0 and IoT, digital control tops are becoming indispensable components of future process plants,” he says.
Beyond IO-Link, dairy plants can become more sustainable via quick-response (QR) codes and remote service, Medlar suggests. “QR codes encode the GEA Global Unique Identification Number and redirects directly to GEA Portal where the customer will find general and technical data about the product (e.g., serial number, valve type, size, spare parts, product pressure, manuals, etc.); strengthening our paperless approach for technical documentation,” he notes. Furthermore, beginning this summer, every hygienic valve and pump will be equipped with a QR code, he adds.
Regarding remote service, Medlar points to condition monitoring and predictive maintenance. “Based on information obtained through sensors installed in our equipment, it could be possible to predict when the equipment is running out of the best performance conditions and therefore plan the next maintenance,” Medlar relays. This, he says, reduces downtime.
Improving energy efficiency through automation is the first step to making dairy plants more sustainable for the future, adds Smith. “We have the technology to achieve this already, with research showing that by implementing existing digital solutions, we can cut carbon emissions by up to 70%. While it is always an upfront cost to install these technologies, the cost advantage of reducing inefficiency and waste is a prudent investment across all industries; and dairy plants are no different,” he states.
Energy and water conservation
A current — and future — aspect of the dairy plant of the future is sure to focus on the all-important energy reduction and water conservation.
Discussing energy efficiency, Smith first mentions renewable energy options like solar panels, wind turbines and anaerobic digesters to generate on-site power. “Further, [dairy processors] can upgrade to energy-efficient equipment and lighting, such as LED lighting, high-efficiency motors, and variable frequency drives to use more efficient equipment that inherently uses less energy.”
Regarding water conservation, dairy processors can install water-efficient equipment and fixtures, such as low-flow nozzles, automatic shutoff valves, and water-recycling systems, Smith adds.
“Implementing water-saving practices in cleaning, sanitation, and other processes, such as using closed-loop systems and optimizing water use also helps to minimize the amount of water that is used,” he explains. “Recycling and reusing water wherever possible, such as using treated wastewater for irrigation or cleaning, is also a great way to improve water conservation.”
Dairy processors can also “monitor and track water usage to identify and address areas of high consumption and help make data-driven decisions when deciding how to invest further in their equipment and infrastructure,” Smith continues.
One path to energy efficiency is setting the pressure down to 4 bars, coming from 6 bars, which can unlock an annual 16% savings in compressor energy, Smith suggests.
Medlar states that less water consumption is achievable via “GEA’s electronic LEFF function in T.VIS valve control tops, which can save more than 90% water and cleaning agents during valve seat cleaning.”
He also alludes to product recovery systems that can remove pipeline residues and “can noticeably reduce clean-in-place (CIP) water consumption and additionally save water as a product ingredient.”
Also, the divisible actuator is “under development for PMO M/2.0 valves used in CIP supply and return lines and will increase efficiency as well as reduce cleaning medium consumption by allowing the separation of the upper and lower valve disc in open position,” Medlar notes.

AI in focus
AI is definitely the biggest buzzword on Wall Street. Evidence lies in the stock of AI semiconductor chip stock Nvidia, which rose 130% in the first five months of 2024. Hence, investors are betting AI will be a big part of the future of society. But how exactly will AI transform the dairy plant of the future?
“As AI is integrated into a number of manufacturing markets, its adoption in the dairy production environment will be no exception,” says Brook Schroeder, P.E., program manager, Mechanical Process Group, Shambaugh & Son, L.P., Fort Wayne, Ind. “This technology has the potential to help plants realize significant improvements in quality monitoring, predictive maintenance and efficiency. However, AI implementation will also require ever-increasing levels of real-time data to feed it. Accordingly, plants will need to be outfitted with more sophisticated instrumentation than ever before.”
Adds Reubin Bricker, BIM/VDC manager for the Planning & Design Department, Shambaugh & Son: “With emphasis on plant design and construction, CAD/BIM software is continually being influenced by AI. For example, ‘Generative Design’ can be used to transform project specific information provided by the designer (such as, code requirements, size constraints, safety concerns, environmental regulations and budget) into limitless design options to best implement all the information simultaneously. AI has a long way to go, but many tools and services are waiting to be utilized today.”
The capabilities of AI should excite the dairy industry, as it offers ways to accelerate processes and improve accuracy, as well as reduce carbon emissions, Schneider Electric’s Smith suggests. He believes predictive maintenance, as well as sustainability and energy management, can benefit dairy processors.
“AI-powered systems can analyze sensor data from equipment to predict when maintenance is needed, preventing breakdowns and optimizing uptime. Similarly, machine learning algorithms can identify patterns and anomalies to proactively address issues before they become problems,” he notes.
In terms of sustainability and energy management, “AI can help optimize energy usage, monitor emissions, and identify opportunities for conservation and renewable energy integration. Machine learning can analyze data from building management systems, equipment, and processes to uncover ways to reduce the dairy plant’s environmental footprint,” Smith suggests.
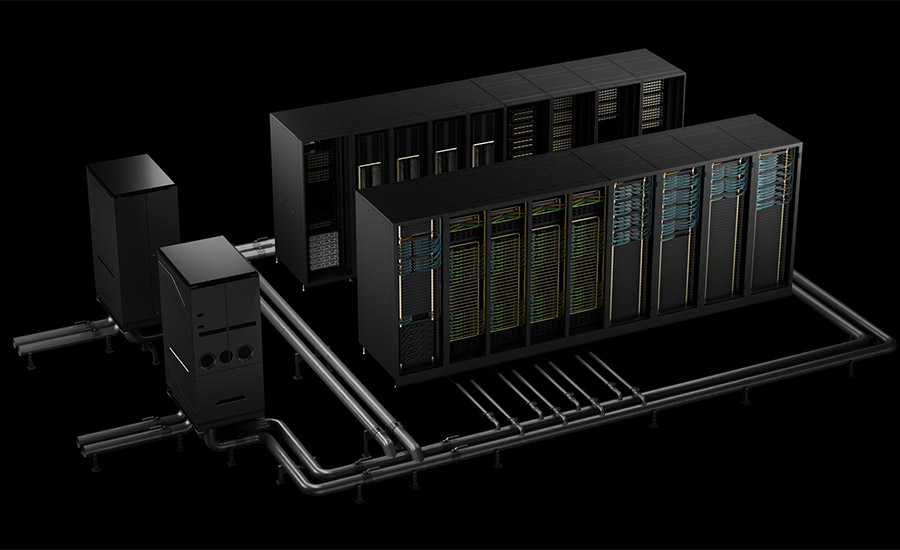
Can goals be met?
With sustainability top of mind for dairy processors, combined with new and exciting technologies on the way, it is likely that today’s dairy processing plant will be much different tomorrow. But this leads to one final question: Can dairy processors meet the carbon emission-reduction goals they have set forth to meet by 2030?
Schneider Electric’s Smith predicts the deployment of new technologies discussed in this article will help achieve 2030 carbon-reduction goals. He acknowledged the “clock is ticking,” but more energy-efficient technologies at every level will make a huge impact.
“A further component to this is process optimization, which can be achieved through the implementation of closed-loop systems to reuse and recycle water, wastewater, and process byproducts,” Smith reveals. “The development of innovative valorization processes to convert waste streams into valuable products, such as renewable chemicals, biofuels, or animal feed, makes it impossible to minimize the environmental impact of the dairy plant.”
Baumer’s Lake stresses the total impact made by all dairy processors wishing to reach sustainability goals will be enormous. “By lowering overall energy consumption, [dairy processors] will make an impact on carbon emissions,” he concluded. “There are several local processing plants, so the effect of saving energy will be felt across the country and will be magnified.”
Looking for a reprint of this article?
From high-res PDFs to custom plaques, order your copy today!