Secondary packaging provides unique challenge for dairy industry
Packaging is an issue of robust importance for manufacturers and brands alike.

Automation has several distinct advantages when it comes to secondary packaging. Courtesy of Waldner North America
Packaging is an issue of robust importance for manufacturers and brands alike, as they continue to look for new and innovative ways to make the end-to-end process more efficient, sustainable, and safe. While this goal is certainly shared across the vast food and beverage industry, the dairy sector faces a unique set of challenges when it comes to secondary packaging.
When first considering the challenges of dairy packaging, most probably correctly assume that maintaining product freshness is the top priority. When it comes to milk, for example, according to the Food and Agriculture Organization of the United Nations, it is highly perishable because of its susceptibility to microorganism growth, leading to the presence of bacterial pathogens.
The spoilage issue has largely been mitigated due to well-established scientific advancements like pasteurization and optimized storage practices. In addition, improvements in primary packaging have also contributed to the overall shelf-life of dairy products. Whether it’s stronger barrier properties or enhanced durability, these advancements have greatly enhanced the overall quality of dairy products in the market.
With primary packaging largely handled, the focus has shifted to secondary packaging. Simply put, secondary packaging refers to the protective packaging that surrounds the packaged products throughout its delivery from the dairy plant to its final destination in store.
Examples of secondary packaging in the dairy sector include folding cartons, corrugated boxes, and plastic crates, which are vital to protecting product durability and safety. In dairy, the main challenge that faces secondary packaging is ensuring that the overall operation is efficient enough to maintain freshness of the product, while also providing adequate protection from transport damage.
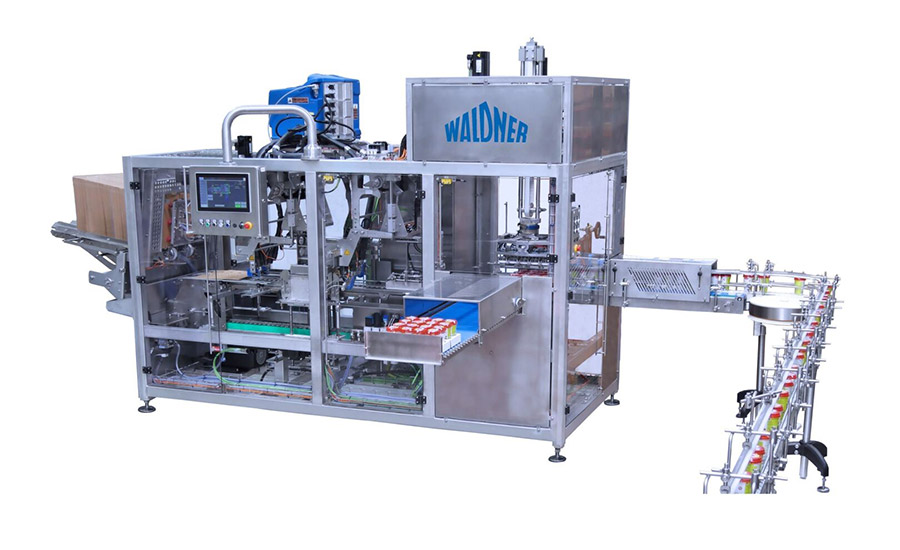
“When you think about dairy, whether it’s milk, ice cream or cottage cheese, any of those things can spoil if they’re in the secondary packaging system for too long,” explains Tom Wiersma, vertical marketing and business development manager, Integrated Packaging Machinery (IPM). “So, if the secondary packaging system breaks down, then the [product] is sitting out there in the environment and is subject to spoilage. The secondary packaging challenge is to get from primary packaging to the refrigerated warehouse in the proper time. To do that requires far more than aspiration. It requires an intentionally integrated and systematized approach to engineering and controlling packaging system uptime.”
All hits, no errors
A key factor in maintaining the overall efficiency of the secondary packaging operation is limiting errors. With such intricate machines and processes, one small hiccup can lead to devastatingly long delays in getting dairy products to their final destination.
“The magic problem in packaging is 100% detection 100% of the time,” says Matthew Gwin, product manager for Boston-based Waldner North America. “That’s not a reasonable goal. Nobody can detect everything at all times. Really at the end of the day, what it comes down to is having a very reliable machine that can run at high efficiency, so the ones that you do need to detect are much less likely to happen.”
Companies like IPM and Waldner North America both specialize in providing automated machinery solutions for dairy packaging, and while they each have unique offerings, they share common considerations when looking to provide outstanding services to their customers. At the top of the list is machine versatility.
“Customers want flexible machinery. A lot of customers seem to be moving toward a regional desire where they want food that seems local and custom, and to do that as a big company you have to be able to have machines that can run a lot of different sizes and looks,” Gwin explains.
With more companies developing unique packaging, they also are launching different types and sizes of packaging materials. For this reason, machines have to be adept when it comes to handling a variety of package types from the same company. This increase in SKUs has placed even more of an enhanced importance on developing machines that can deal with multiple materials and shapes.
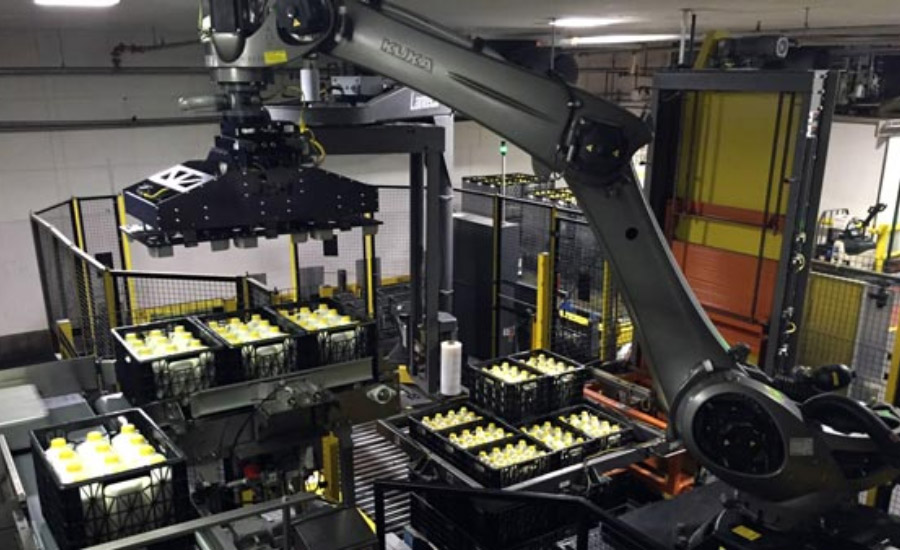
“Taste options and serving-size options are driving the SKU count higher, so our packaging automation solutions now have to accommodate different package sizes, different package weights, and different kinds of food,” Wiersma says. “So on a cheese line, there’s going to be shredded cheese, string cheese, cubed cheese, and sliced cheese all on the same line.”
Automation impact
Hand in hand with this is the continued shift toward automation. A top priority for secondary packaging machinery providers, automation helps reduce errors, improve hygiene, and increase overall equipment effectiveness (OEE).
“Automation and control is a very important driver moving forward,” notes Wiersma. “If done well, it reduces staffing needs, it improves the performance of packaging in the last mile and it reduces the cost of utilities.”
Automation also lends itself into sustainability. While the first area of focus when it comes to sustainable packaging typically is the package itself, secondary packaging machinery can also make the packing process more eco-friendly.
“People always think about sustainability in terms of emissions from a package or recycling of a package, but where [Waldner North America] can help is with the efficiency of the machine,” Gwin says. “There’s cups that don’t fill right, there’s things that get punctured or broken, there’s product that can spill. That efficiency [and error prevention] is where we see a lot of sustainability gains.”
“Sustainability isn’t just about packaging materials,” Wiersma notes. “It’s also about energy needs, and the impact that has on the global environment.”
With all the benefits automation brings, some companies are still hesitant to fully implement it in their machinery due to the training it requires. While it would be natural to assume that increased automation reduces the need for operator training, that isn’t necessarily the case.
“The knowledge base and training is the biggest hurdle [to automation],” says Gwin. “When you’re moving from manual labor to automation, obviously you can reduce your headcount in your factory, but that knowledge base has to grow in order to maintain that equipment and keep it running. The knowledge base to manually load a carton is pretty low, but the knowledge base to maintain a cartoner is higher.”
Regardless of where companies fall when it comes to embracing automation, it’s clear that secondary packaging will continue to be a key area of importance for dairy manufacturers.
Looking for a reprint of this article?
From high-res PDFs to custom plaques, order your copy today!