Dairy plant warehouse automation picks up speed
Dairy processors are embracing increasingly sophisticated machinery, software and systems in the move to optimize warehouse operations.

Photo courtesy of N-sky via www.gettyimages.com
Technologies are taking hold in dairy-production warehouses. The prospect of enhancing efficiencies and productivity while reducing labor expenses is resulting in the greater incorporation of automated systems by dairy processors while helping to trigger the development of newer designs.
The global warehouse automation market is forecast to reach $30.7 billion by 2028, with a compound annual growth rate of 14.2% from 2021 to 2028, reports New York-based Polaris Market Research. The North American sector will likely have the highest market share, owing to the increasing adoption of robots and cutting-edge technologies, particularly in response to the higher labor costs in the region and the increasing number of accidents in industrial workplaces, Polaris states.
Automated storage and retrieval systems (AS/RS), meanwhile, account for the largest technology market share, Polaris states. An AS/RS is a combination of equipment and controls that operators leverage to handle, store and retrieve materials with precision, accuracy, and speed. Solutions vary from smaller automated systems to larger computer-controlled storage/retrieval systems that processors can integrate into their manufacturing and/or distribution processes.
Keep pace with the competition
Such technologies are becoming a necessity for companies seeking to remain competitive in their respective supply chains, says John Hinchey, vice president of sales for Westfalia Technologies Inc., a York, Pa.-based provider of warehouse technologies. He notes that automation also can provide dairy processors with such benefits as efficient and accurate order fulfillment, real-time inventory accuracy, greater productivity, efficient material flow, and optimized storage density.

Technology developers typically implement specific AS/RS designs in accordance with the unique needs of each processing facility, Hinchey says, with systems often varying due to different product types and packaging sizes.
Warehouse operators also are managing more parts of their operations with advanced technologies, says Gijo George, director, major accounts for Yale Materials Handling Corp., a Greenville, N.C.-based developer of materials handling equipment. He notes, for instance, that newer operator assistance systems provide real-time information about the equipment and operating environment. Technologies also are enabling processors to automatically adjust lift truck performance in accordance with proximity to pedestrians and obstacles, load weight, equipment status, and location-specific rules, George says.
“This technology can work to automatically slow down lift trucks as they approach the end of an aisle, an intersection, another piece of equipment or obstacle,” he states. “It can limit speed in designated zones, prevent access to pedestrian-only areas, proactively reduce speed when traveling around corners to avoid upsetting stability, and prevent trucks from moving loads that exceed weight threshold through hydraulic lock-out.”
In addition, telemetry systems, which automatically measure and transmit data wirelessly from remote sources, can further enhance productivity by providing the information that helps managers prevent unplanned downtime and increased costs, George says. The technology, for instance, can trigger alerts in accordance with hazardous driving behaviors, such as excessive speed or impacts, he states.
“Having access to this kind of data allows organizations to isolate and work on remediating problem areas and reinforce best practices to promote safety,” George notes.
An emphasis on efficiencies
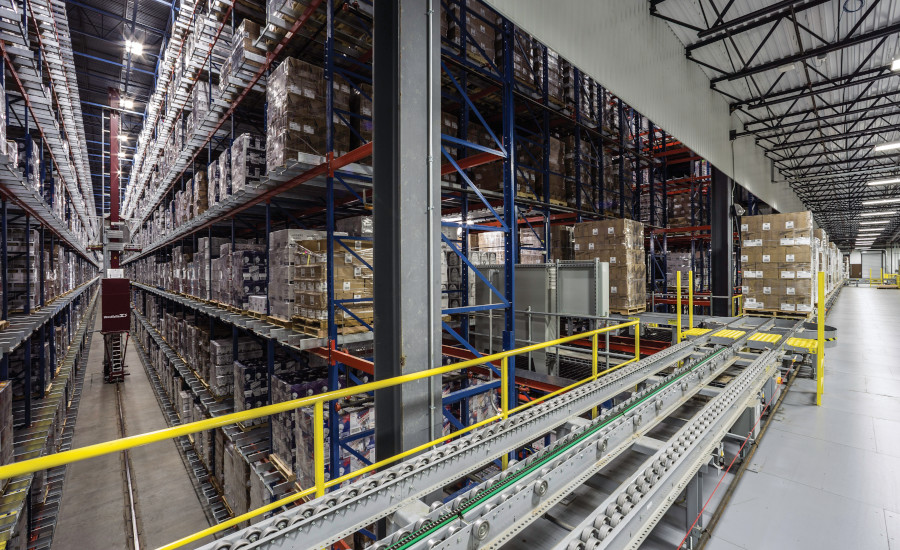
It also is important that operators seamlessly integrate warehousing, storage, and distribution functions to achieve greater productivity and efficiencies, says Mike Stein, vice president of marketing and product management, automation, and packaging technologies platform for Signode Industrial Group LLC, a Glenview, Ill-based transit packaging provider.
“Automated operations that are designed, deployed, and maintained properly equal greater control over labor costs, material handling costs, spoilage costs, and the costs related to maintaining temperature control in large facilities,” he states.
Newer warehouse solutions, meanwhile, including next-generation software, are enabling operators to better integrate legacy systems with more automated lines, Stein says. The integration of enterprise resource planning and order management systems is resulting in better inventory control, product tracking, and real-time connection between the business and warehouse systems, he states.
In addition, the use of robotics is rising following “massive deployments” in response to COVID-19, reports Mordor Intelligence, a Hyderabad, India-based market intelligence and advisory firm.
“The COVID-19 pandemic has led warehouse operators to consider accelerating their timetables to adopt automation and robotics,” Mordor Intelligence states. “Those who have successfully deployed also depicted the creation of safer workplaces by reducing interactions among workers while simultaneously enhancing productivity.”
Indeed, the adoption of autonomous mobile robots technology that eliminates significant nonproductive walking time in warehouses has progressed from early-stage pilots about four years ago to multiple at-scale deployments today, states McKinsey & Co. Inc., a New York-based management consulting firm.
“Fueled by venture capital over the past five years, the automation industry has seen increased availability of new warehouse automation innovations, supply-chain-as-a-service models, and technology that integrates multiple solutions,” the firm notes.
An effective warehouse management system also will help increase the number of products that processors are efficiently producing while enabling the tracking of each item so operators can trace contaminated products back to the source, says Gernut van Laak, global food and beverage solutions manager for ABB Ltd., a Zurich, Switzerland-based provider of automation technologies.
It important, he notes, that the systems provide the necessary transparency to bring operational data into context.
“Receiving information in real-time makes decision-making much easier and faster by giving processors more time to think about what to do,” van Laak states.
An antidote to worker shortages
The ability of dairy processors to automate more warehouse functions is resulting in lower labor expenses as well, analysts state.
“Never before has the competition for warehouse and fulfillment labor been so fierce, strongly driven by sustained growth in B2C channels,” reports McKinsey & Co. The firm notes that while employment levels across U.S. distribution centers are at all-time highs and wages have risen to well above $18 an hour, “attracting and retaining warehouse employees remains elusive. In the short term, strategies such as bonuses, accelerated pay raises, and tuition reimbursement are helping. But the long-term implications of a high reliance on labor are clear: Automation in warehousing is no longer just nice to have but an imperative for sustainable growth.”
Meanwhile, more technologies designed to enhance warehouse efficiencies while reducing labor or enabling workers to become more effective are becoming available as well, says John Tippmann, III, vice president of sales strategy for Tippmann Group, a Fort Wayne, Ind.-based owner, operator, and builder of cold storage warehousing. Such equipment includes automatic guided vehicles that can complete simple tasks and enable workers to focus on more complex matters, narrow-aisle turret systems that allow employees to be in a heated cab and pick pallets without interference from other lifts, and warehouse management software that enables real-time activity tracking, he states.
“Having a robust warehouse management system so employees are not waiting or are limited on the speed that a system can process what they are accomplishing in real-time makes a significant difference,” Tippmann notes, adding that “whatever can be done to help reduce the amount of labor needed to effectively run an operation is key.”
Robotic lift truck technology also is advancing to accommodate a greater range of horizontal transportation and vertical storage tasks, George says.
“Many customers want to automate as much as they can due to the challenge of finding enough applicants to fill open positions and the high worker turnover in warehousing,” he states.

Hiring and retaining qualified lift truck operators is a fundamental challenge for dairy operators, as it increases both the burden of training new employees and the risk of inexperienced personnel deviating from site-specific safety protocols, George says. He notes, however, that warehouse managers can delegate repetitive tasks to robotic lift trucks while leaving more engaging, value-added tasks for workers.
“Creating a division of labor between employees and robotics leverages the best capabilities of each, and helps reduce labor dependency, maximize productivity and improve employee retention,” George states.
Decision-making can be difficult
Despite the advent of increasingly functional and efficient warehouse technologies, it can be arduous for processors to pinpoint and implement the most advantageous solutions for their specific circumstances, analysts say.
“There are unique differences to every single operation in the cold storage and processing industry,” Tippmann states. “What works for one company may not work for the other.”
The lack of necessary space in many cold storage facilities, for instance, may necessitate the development of new warehouses or expansion of existing ones.
“Longer than normal lead times for materials and the growing need for construction has some companies maxed out of what they can produce,” Tippmann says.
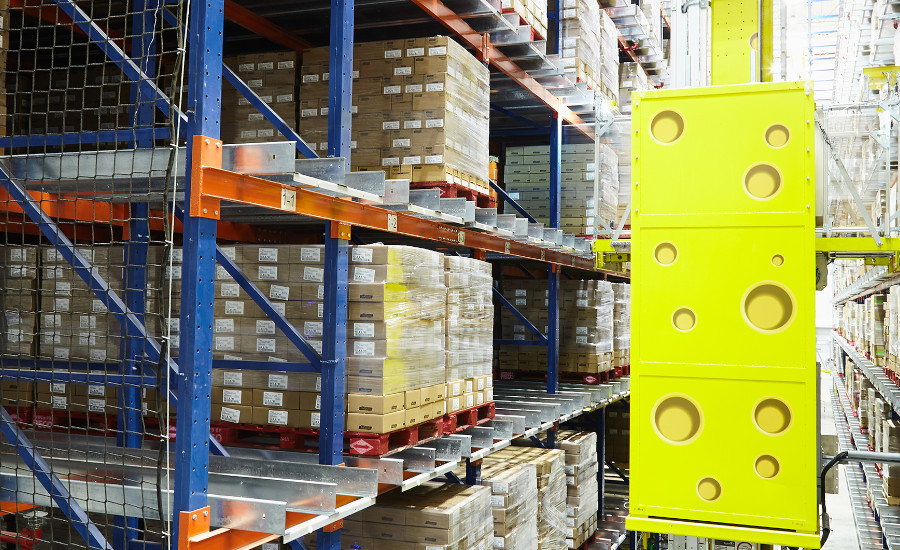
It also is crucial that processors understand the “ins and outs” of their systems to leverage the most effective equipment, Hinchey says, noting that operators should analyze such elements as space availability, temperature control needs, and product types.
The increasing cost of cold storage can be burdensome as well, he states, but he notes that the AS/RS vertical design enables companies to operate on smaller land plots, which makes it more likely they can locate closer to their customers.
For best results, processors should partner with suppliers that have a strong dairy industry track record and an established process for implementing specific applications, Stein says.
“It’s not just about the technology, as it doesn’t live in a silo,” he states. “Knowledgeable partners possess the expertise to design systems based on a needs analysis, to install an integrated system, and to plan for the pro-active maintenance requirements.”
Tippmann agrees, adding that a design-builder that understands cold storage construction, especially regarding food and distribution, can provide valuable guidance. That is important, as similar shells of a warehouse can have two completely different operations inside and require different infrastructures.
“The needs for each company are very specific,” he says.
Dairy processors’ experience in using warehouse technologies, meanwhile, also will enable the operators to better pinpoint the appropriate automation for their facilities, van Laak says. An important consideration, for instance, is choosing the right systems to connect different generations of plant equipment that may be 40 years apart and from varying suppliers, he states.
“There can be automation islands where the machinery is not talking to each other or exchanging information,” van Laak adds. “In such instances, however, it may be better to just move to a new-generation machine.”
Looking for a reprint of this article?
From high-res PDFs to custom plaques, order your copy today!