Equipment
Maer develops latest generation of high-performance cutters
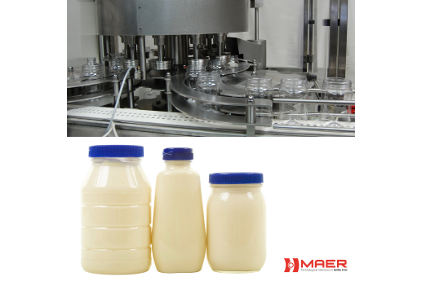
By Maer
Maer, a worldwide reference in the sector, has developed the latest generation of high-performance cutters with the WM500 TC10 rotary system.
In recent years, the packaging industry, always in constant evolution and requiring efficient responses to demands, has encountered a problem that calls for a solution: improved production of wide-mouth PET jars for mayonnaises and sauces.
Thanks to its resistance and durability, glass has traditionally been the only efficient response for conserving this type of products. But today’s needs of manufacturers and consumers are making PET packaging the most cost-effective and attractive solution.
Consequently, the manufacturing technology of "blow-trim" type plastic jars marks the difference in improving production speed, reducing purchasing costs of materials and investment in machinery and permitting the use of market-standard blown performs in the same mould.
Thinking of the bottler or manufacturer who produces in the same bottle-blowing machine or line wide-mouth jars with a final neck of between 60 and 99 millimeter, Maer’s WM cutting system offers outstanding versatility in admitting the pass-through of other formats which do not require cutting and without needing to bypass the cutting machine.
In this respect, Maer now introduces 4 new lines for an important project in Kazan (Russia) consisting of jar-blowing units, bulk package conveyors to storage silos and positioning machines which feed the 4 Maer model WM500 TC10 rotary cutters, with a capacity for cutting 14,000 receptacles per hour in formats from 250 to 900 cc.
About Maer
With over 20 years’ experience in the plastic bottle packaging industry, MAER offers technological solutions which have made it a company of reference in the sector. Its proposals, cost-effective, flexible and adapted to the needs of each project, include the design and manufacture of rotary dome cutting machinery and finishing of bottles made by extrusion blowing in PE, HDPE, PP, PVC and PET.
SOURCE: Maer
Looking for a reprint of this article?
From high-res PDFs to custom plaques, order your copy today!