Condition Monitoring Makes for Timely Maintenance
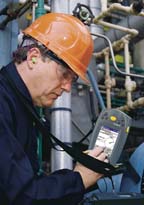
During the 1970s most plants established some type of preventive maintenance program. By the 1980s well-run operations were employing predictive maintenance strategies and, by the 1990s, diagnostic tools and software were providing maintenance personnel with machine condition information.
Today, the focus of maintenance approaches within industry clearly has shifted from "reactive" to "proactive." In an ideal world, every plant would make use of all the best new related technologies for enhancing machine reliability. In the real world, options may prove limited, either by staff expertise or program costs.
"Condition Monitoring" (CM) represents one of the more practical approaches for operations seeking to reap the rewards of proactive maintenance. CM is a strategy whereby physical parameters (such as vibration, temperature, pressure, or flow) are measured regularly to determine equipment condition. This procedure makes it possible to detect machine and component problems before they can result in unexpected downtime and the high costs associated with interruption in production.
This process of monitoring further serves as a platform for implementing an effective "Condition-Based Maintenance" (CBM) program, whereby maintenance, inspection, and overhaul of plant machinery are scheduled on the basis of machine condition.
In this way, scheduling of maintenance activities relies upon condition data instead of the calendar. The goal is to trend and analyze data in order to identify troublesome conditions and detect early stages of component degradation in order to take remedial action to prevent failures, and reduce unanticipated downtime.
Basic instruments are available to equip users for a low-cost CM program. These can assess and report on vibration, temperature, and other specific parameters relating to the health of equipment. More advanced CM tools encompass online surveillance monitoring systems and software delivering fully automated machinery monitoring for up-to-the-minute information and optimized operation of key production assets.

Vibration as a key indicator
Many machinery problems manifest as vibration, which is widely considered the best operating parameter to judge a machine's condition. Vibration can detect machine fault conditions such as unbalance, misalignment, oil film bearing instabilities, roller bearing degradation, mechanical looseness, structural resonance, soft foundation, misalignment, rotor bow, and cracked rotors, as well as many other fault conditions. Vibration measurements are also quick and fairly non-intrusive since the operating equipment is not disturbed.Measuring "overall vibration" (the sum of all vibration within the frequency range of the vibration instrument to provide one "overall" vibration level) can be used to determine if there is an impending equipment problem by detecting an increase in overall vibration.
Typically, the user compares the overall vibration level to the baseline value and if the level becomes too severe, action can be taken before equipment failure occurs. There are also industry standards available that provide vibration severity levels for specific types of equipment and operating speeds that can be used as a guideline to establish equipment vibration severity.
(Although "overall" vibration can provide a quick assessment of the health of equipment, there are limitations to "overall vibration" measurements, because it lacks the detailed information to diagnosis the problem.)
There are many hand-held vibration monitoring tools on the market today that can do the job, ranging from low-cost vibration pens and overall vibration meters to more sophisticated portable data collectors and related instruments that combine compact size with data storage capabilities to provide an inexpensive starting point for a periodic CM program.
Most "overall" vibration meters (with a fixed monitoring frequency band) measure velocity over a frequency range of 10 Hz to 1 kHz, which is considered the best range for judging rotational and structural problems (imbalance, misalignment, looseness, and stress applied to components).
More sophisticated portable data collectors/analyzers collect and store machinery vibration data over a much broader and higher frequency range (typically up to 20 kHz.) and display high resolution FFT frequency spectra and time domain waveforms on an LCD screen. Collected vibration measurements can be analyzed on the spot or downloaded to a host computer's database management program for analysis and long term trending. Portable data collectors/analyzers can be used not only to detect vibration problems but to diagnose specific machinery faults due to their FFT spectrum analysis capabilities.
Many new users of vibration technology sometimes overlook the tradeoff between a simple overall low-cost meter and more sophisticated portable data collector/analyzers with FFT spectrum capabilities. Although a simple overall vibration meter is easy to use and requires little training, it lacks the spectrum capability required to diagnosis the vibration problem. Portable data collector/analyzers with FFT spectrum capabilities can provide much more information to diagnosis the machinery problems; however, users must be properly trained in vibration analysis.
The data collector can be used to take vibration measurements at each designated point with a temporarily attached probe or sensors permanently attached to the machinery. Other CM measurements (process pressure and flow) can likewise be read from instruments and entered through a data collector's keypad.
Another key parameter whose regular monitoring can shed light on machinery conditions as part of a CM program is temperature. This is a useful indicator of mechanical condition or the load applied to a specific component (such as a thrust bearing).
For example, as a thrust bearing fails, friction causes its temperature to rise. Installing thermocouple sensors in the housing of a bearing and measuring temperature changes within the bearing or lubricant can send a signal about problems beginning to develop. Maintenance can then be scheduled before a more serious and expensive condition occurs.
Online surveillance monitoring systems can complement the efforts, facilitating a proactive approach to reliability with round-the-clock monitoring of machinery, regardless of location. These systems collect data continuously or over a predetermined data-collection frequency, from permanently installed sensors, then relay the findings to a host computer for analysis.

Bearing defects signal trouble
In addition to monitoring the overall condition of a machine, CM technicians would do well to direct their attention to detecting the condition of a machine's bearings. The reason: Most machine problems eventually cause bearing defects, which become virtual "mirrors" for the problems.A bearing may fail due to quality, improper lubrication, contaminated lubrication, heavier loading than anticipated (caused by other machinery problems like imbalance, misalignment, bent shaft), improper handling or installation, surface fatigue, or other factors.
The "good news" is that a failing bearing produces noise and vibration signals. If detected and properly analyzed, these signals provide maintenance personnel adequate time to correct the cause of the bearing problem (effectively extending the bearing's service life) or, if necessary, time to replace the bearing during scheduled downtime before complete failure.
When new, bearings exhibit virtually no vibration (assuming they were properly installed and lubricated). However, over time, bearings may begin to degrade. As they do, they develop unique vibration patterns that enable a CM technician to detect the presence of a problem and to determine progression of damage. (It is important to note that a bearing's failure point varies. The type of bearing, lubrication, load, speed, and application all will play roles.)
Our experience supports a two-step approach to detecting and analyzing bearing faults: early detection and in-depth bearing fault analysis.
Fault Detection. This should be performed as easily and reliably as possible. Workers can program the vibration monitoring hardware and database to generate an alarm when bearing conditions change. Alarms then will bring suspect bearings to the attention of maintenance reliability personnel, who can perform in-depth analysis to confirm the fault, determine severity, and, if possible, determine root cause. Detection systems must be structured to communicate fast, accurate measurements. Proper alarm settings are critical for generating alarms when bearing conditions change.
Diagnosis/Analysis. After an alarm notifies reliability personnel of a change in bearing condition, in-depth analysis should be performed to confirm the fault, determine severity, and to diagnose root cause. Trends from original "detection" measurements should be analyzed and additional measurements may be performed at various probe orientations to obtain more analysis information.
As all these and related avenues suggest, there are many ways to implement CM approaches for the good of machinery and productivity. But the "human" factor should neither be underestimated nor overlooked. Routine operator and maintenance technician oversight and observations can yield valuable "subjective" data for the good of the cause.
Regardless of the extent to which a CM program is fully realized, its success ultimately will be linked to full implementation of a CBM strategy. Otherwise, potential benefits may fall short and optimum return on investment and effort may not be achieved.
Looking for a reprint of this article?
From high-res PDFs to custom plaques, order your copy today!